Abbiamo visitato l’e-plant di FPT Industrial: viggio dentro la fabbrica dell’e-power
Vi raccontiamo sistole e diastole del cuore elettrico di Iveco. L’e-plant di FPT Industrial nei più intimi dettagli. Dalla preparazione dei kit, all’assemblaggio, al fine linea. Delle 74 celle di prova, 5 sono destinate ai motori centrali, tipicamente per i Daily, agli assali elettrici e all’e-CD. La chimica Nmc applicata agli autobus prevede tanti cicli […]
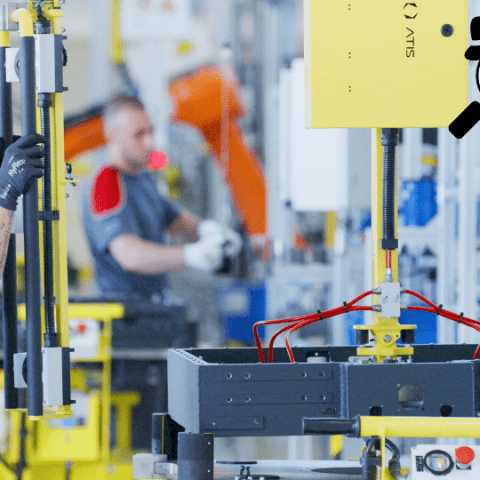
Vi raccontiamo sistole e diastole del cuore elettrico di Iveco. L’e-plant di FPT Industrial nei più intimi dettagli. Dalla preparazione dei kit, all’assemblaggio, al fine linea. Delle 74 celle di prova, 5 sono destinate ai motori centrali, tipicamente per i Daily, agli assali elettrici e all’e-CD. La chimica Nmc applicata agli autobus prevede tanti cicli e C-Rate bassi
Due anni di attività, un’attualità targata captive, un futuro aperto alle collaborazioni con gli Oem (come quella in essere per la Maserati Folgore). È il ritratto dell’e-plant di Torino, la gigafactory nella quale convergono le competenze di elettrificazione di FPT Industrial. Vi accompagneremo passo passo nella genesi di batterie e assali elettrificati.
Daniele Pozzo, manager in ambito marketing e product portfolio, ci fornisce le credenziali di accesso, prima di avventurarci tra reparto produttivo e testing. «Per quanto riguarda i sistemi di energy storage, ci focalizziamo su due elementi. Il primo, dall’inaugurazione dell’e-plant, nell’ottobre 2022, è l’Ebs37, sigla che identifica l’energia installata in kWh della batteria. A Torino assembliamo i moduli e gli accessori come cablaggi, Bms (Battery management system), housing e coperchio. FPT mantiene sotto il proprio controllo lo sviluppo, la scelta della chimica e la gestione del software. L’R&D center di Coventry ci consente di sviluppare algoritmi per ottimizzare l’utilizzo della batteria agli ioni di litio, tecnologia Nmc, 37 kWh, con una densità di 140 Wh/kg. Ci affidiamo a una struttura a moduli, con cui completiamo il pacco batterie. Microvast produce le celle e le assembla all’interno dei moduli. Il secondo, fratello maggiore di questo pacco batteria, è l’Ebs69, fedele all’Nmc e montabile in parallelo fino a un massimo di 9: le caratteristiche, il numero di cicli e la missione sono riconducibili all’autobus urbano. La densità energetica è tra le più alte sul mercato (178 Wh/kg)», ci spiega. E le istanze di sicurezza? Tra il 2022 e il 2024 è cambiato il livello di safety.
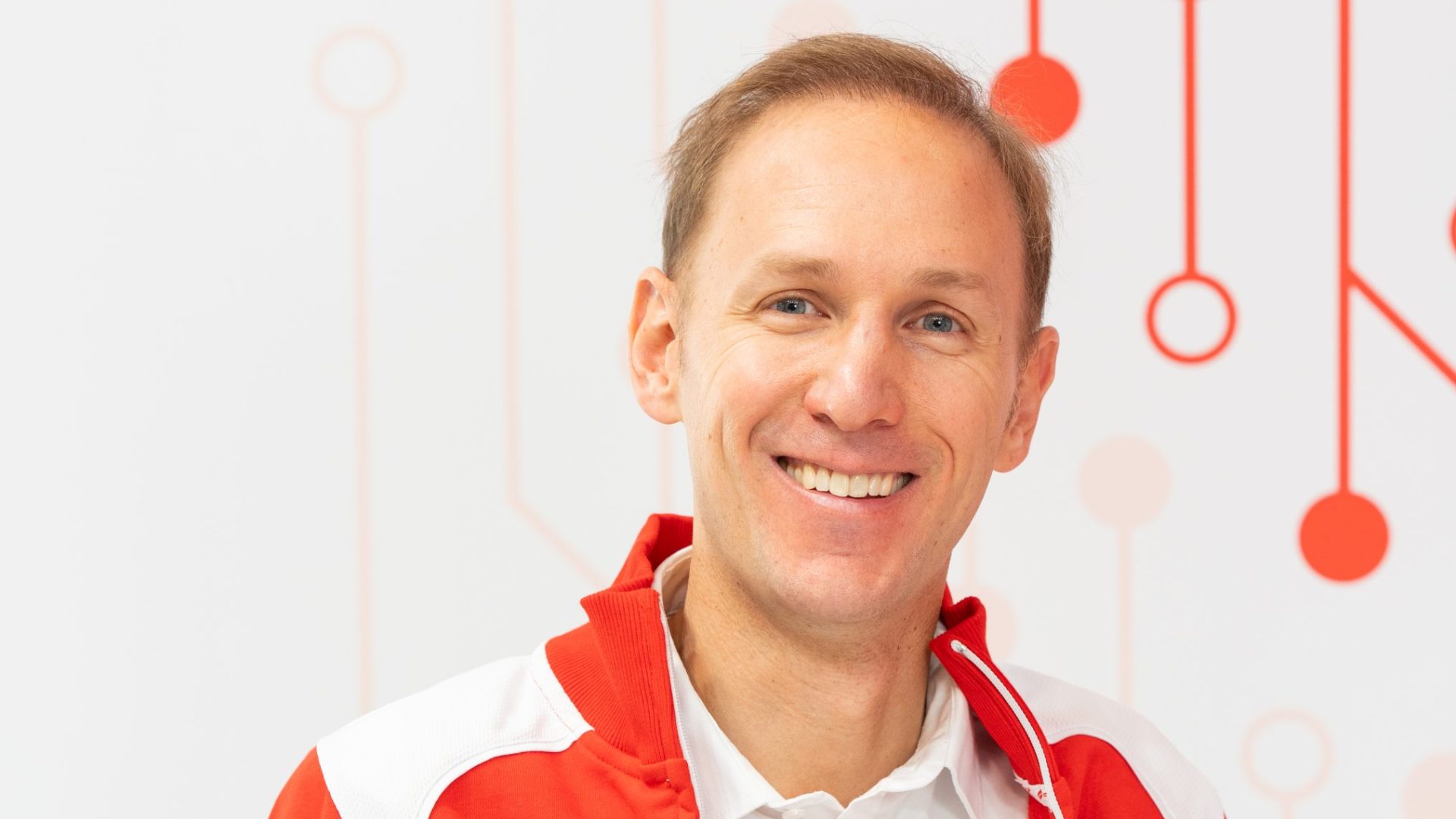
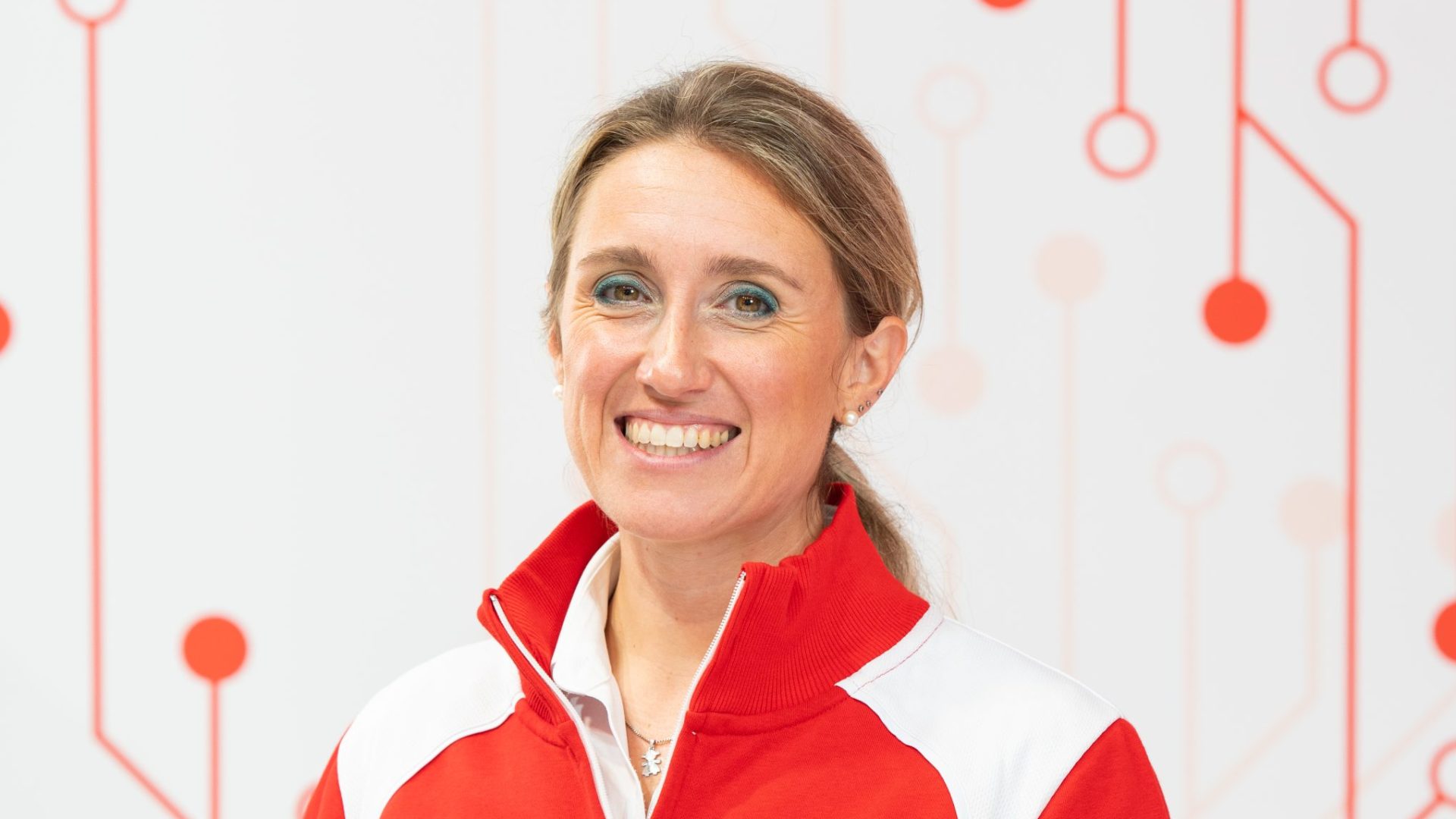
Le batterie dell’Iveco Daily MY 24 (eBS 37 Evo) sono compatibili con la normativa Ece R100.3 di thermal runaway. Queste batterie hanno anticipato le prescrizioni normative, grazie al sistema di detecting e all’hardware interno. Come nel baseball, passiamo da una base all’altra. Daniele Pozzo si sofferma sui modelli nella hall. «All’ACT Expo abbiamo portato l’eAX 840-R, che trovate abitualmente in esposizione. Vedete la central drive, per il Daily, che chiamiamo Ecd140. I due propulsori posteriori e anteriori della Maserati Folgore sviluppano rispettivamente 600 e 300 kW, per consentire un’accelerazione da zero a 100 km/h in meno di 3 secondi».
Interviene Alice Orsi, responsabile marketing ePowertrain e product portfolio, che ci accompagnerà da qui in poi. «La central drive è montata nel mezzo del veicolo e porta la trazione al posteriore, con una cascata a ingranaggi, che permette l’uscita. L’e-axle è una soluzione rigida, che arriva direttamente alle ruote. Infine, abbiamo l’eCD, oggetto sospeso che porta la trazione alle ruote tramite i semiassi convenzionali».
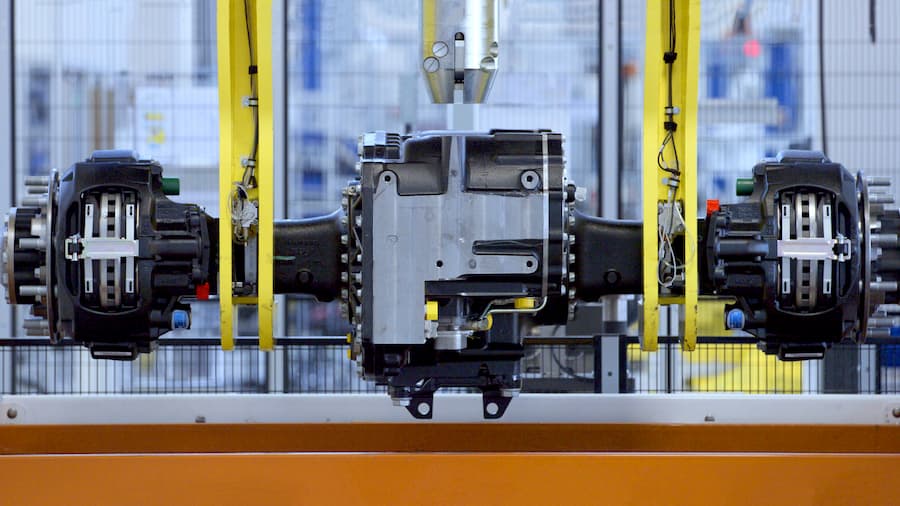
Capacità e assemblaggio in casa FPT Industrial
Pozzo puntualizza le potenzialità e le aspettative dello stabilimento. E sulla finestra applicativa sulla quale si affaccia. «Ha una capacità produttiva di circa 50.000 propulsioni elettrificate all’anno. Si è pensato fin da subito a una soluzione modulare e scalare. Siamo preparati a una forte crescita dei nostri clienti, soprattutto nella seconda parte del decennio, e saremo bravi ad assecondare la domanda, cercando di saturare gli impianti produttivi. Questo è il polo dove abbiamo concentrato le attività di energy storage e di propulsione elettrica. Insomma, è una gigafactory, che noi intendiamo come quel luogo dove, sommando i kWh delle batterie, moltiplicati per i pacchi batterie prodotti in un anno, si supera il GigaWattora. In questa sede, infatti, la capacità produttiva lo supera abbondantemente (sopra 1,5 GWh). Rispetto al passenger car, il settore industriale ha un ordine di grandezza in meno. Ricordiamoci che per ogni autobus, equipaggiato a multipli di 5, 7 o 9, stiamo installando qualche centinaio di chilowattora. Ci sono delle variabili non ancora definite, una di queste è il prezzo dell’idrogeno. Per quanto riguarda le batterie dei pesanti, Iveco si avvale della collaborazione di Proterra. Siamo partiti dalle due aree di maggiore take rate, i commerciali leggeri e i bus».
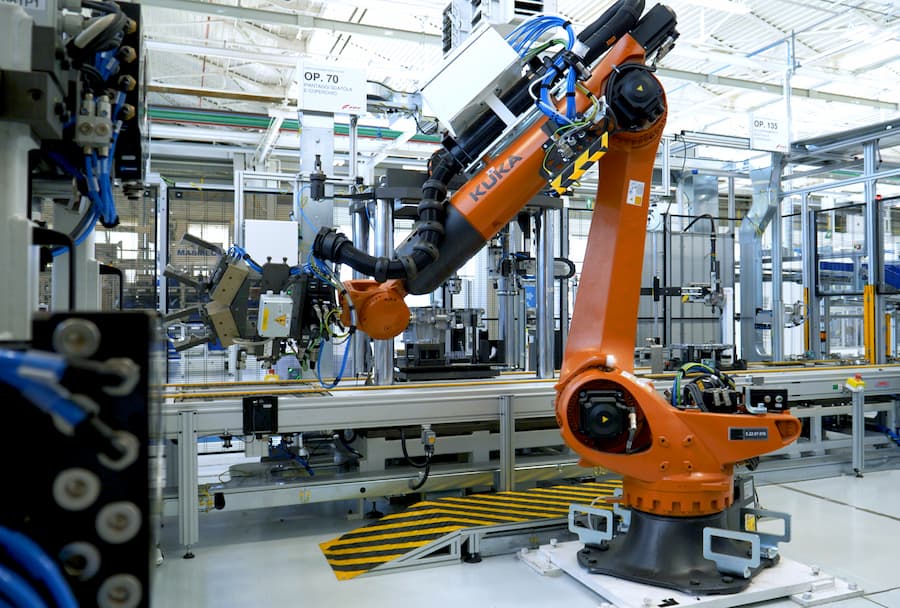
Alice Orsi, come dicevamo, ci prende in consegna per guidarci tra le cinque linee di produzione, dedicate all’assemblaggio dei prodotti elettrici. «Questa fabbrica è divisa in tre aree. Un po’ meno della metà della superficie è dedicata all’immagazzinamento e alla preparazione dei kit; quindi, l’assemblaggio vero e proprio; il fine linea, dove testiamo il cento per cento di quello che facciamo, sia per quanto riguarda le batterie, che il mondo propulsivo: assali, Edu (electric driving unit), central drive. La prima linea è quella della eBS37, poi quella delle batterie, infine gli assali, i central drive e gli assali passenger car. Linee progettate da zero grazie alla realtà aumentata, fin dall’area fornitori. L’IA aiuta le operazioni di assemblaggio».
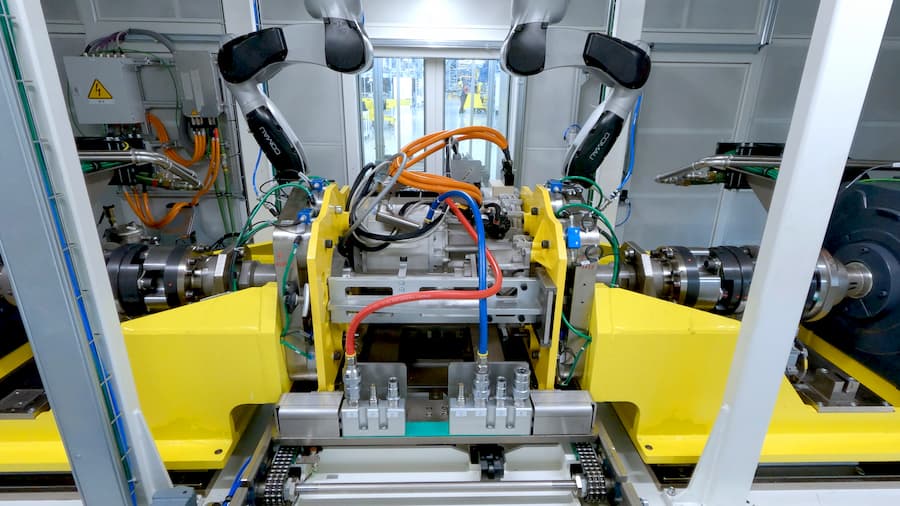
Non è un reparto come un altro, come esplicita sempre Orsi. «I circa 200 addetti sono high-skilled e più di una volta al mese seguono una formazione in gran parte dedicata alla sicurezza. I sistemi di lavoro premiano le competenze ed esonerano le attività fisicamente stressanti. Per questo sono presenti sollevatori pneumatici e oleodinamici che svolgono quelle attività ripetitive che possono trascinarsi negli errori di produzione. Le macchine che svolgono le misurazioni, col sistema pick to light, ci indicano dove prelevare l’esatto spessore da montare nell’assale per garantire il precarico corretto. Ci sono sistemi che agevolano e movimentano, come i veicoli a guida autonoma (Avg), che muovono i pallet tecnologici per tutta la linea, seguendo le tracce blu sul pavimento, e sistemi di sicurezza, le ‘thermal camera’, che osservano in continuazione quello che avviene sulla linea di produzione. Monitoriamo il cento per cento dei componenti che montiamo dentro ai nostri assemblati, tramite data matrix, tracciabilità a 360 gradi, batch code, pick to light, elementi di un plant industry 4.0 e carbon neutral. Nella prima zona di assemblaggio delle batterie preleviamo l’housing e lo disponiamo sui carrelli gialli che accompagneranno il pacco batteria per tutta la linea di produzione. Le prime operazioni sono quelle accessorie, il montaggio del cablaggio a basso voltaggio e del cooling plate, il sistema di raffreddamento, al cui interno passa una miscela di acqua e glicole, e la Battery disconnect unit (Bdu). Ci muoviamo quindi verso una stazione automatizzata, in cui l’operatore si limita a posizionare il carrellino. Ci sono due robot antropomorfi: uno è demandato allo spalmaggio della pasta termica tra gli strati del pacco batterie. L’altro è smart, rileva le dimensioni del pacco batteria e posiziona al suo interno i moduli prelevati, la cui tensione è stata testata».
L’italianità dell’ingegner Orsi si esprime nella seguente metafora: «Possiamo immaginare il pacco batteria come un tiramisù: abbiamo il cooling plate, uno strato di pasta, 8 moduli (i biscotti), e ancora cooling plate, strato di pasta termica, e 8 moduli: è su due layer, 8 moduli e 8 moduli».
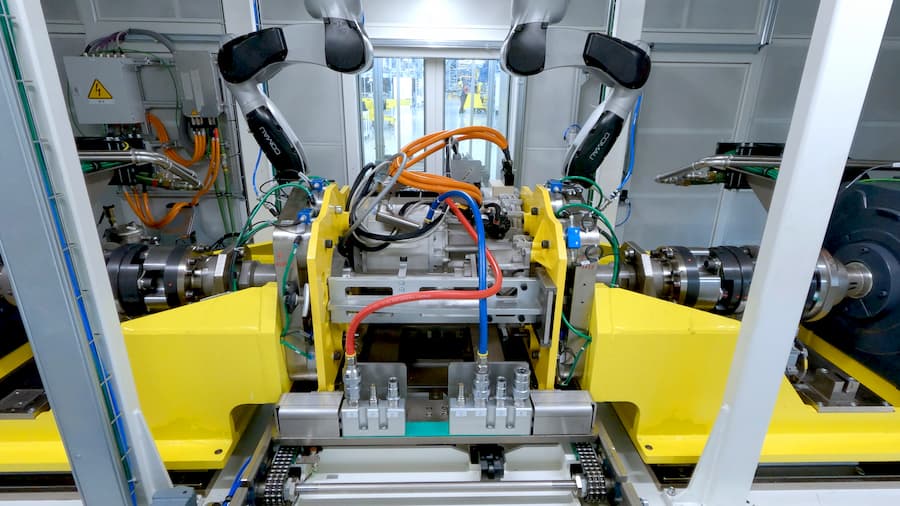
Sulle linee con sicurezza
Proseguendo nell’itinerario manufatturiero troviamo le stazioni gemelle, che ripropongono attività svolte in altre stazioni, in ragione del fatto che il battery pack si compone di due strati. Mentre il cuore della linea a oggi era uno solo (la linea è in espansione con un’altra stazione identica), questa stazione permette di creare il secondo layer di moduli. Qui c’è un’attenzione particolare alla sicurezza, essendo dedicata al montaggio delle busbar, le barre di rame che connettono i moduli tra di loro e permettono di ottenere il corretto serie-parallelo del pacco batterie. L’operatore dispone di un tappetino isolante e di tool che consentono di evitare le dispersioni e di entrare in contatto con l’alta tensione. Nella stazione successiva si prepara il secondo strato di cooling plate e lo si invia alla stazione centrale. L’espansione della linea permette di accrescere la capability e di fronteggiare l’aumento della richiesta. Non si deve più ritornare alla stazione centrale per il secondo strato di moduli e lo si sdoppia in una stazione identica. La seconda parte della linea delle batterie consente di posizionare un altro giro di busbar, avvitare il secondo layer di moduli, di installare il Bms e il cell monitoring controller. L’operatore si occupa anche di effettuare le connessioni dei cavi che permettono il passaggio delle informazioni al sistema, che legge le tensioni e le temperature del pacco batteria, e le comunica al Bms, che adotta le strategie per applicare il corretto condizionamento e gestire i flussi energetici. A partire dall’EBS37 Evo, hardware e software del Bms sono disegnati in casa.
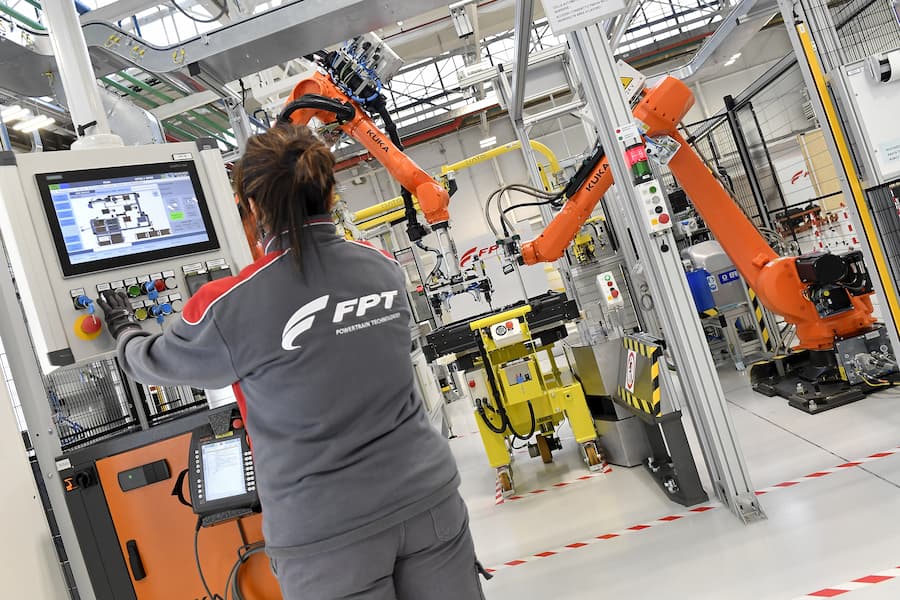
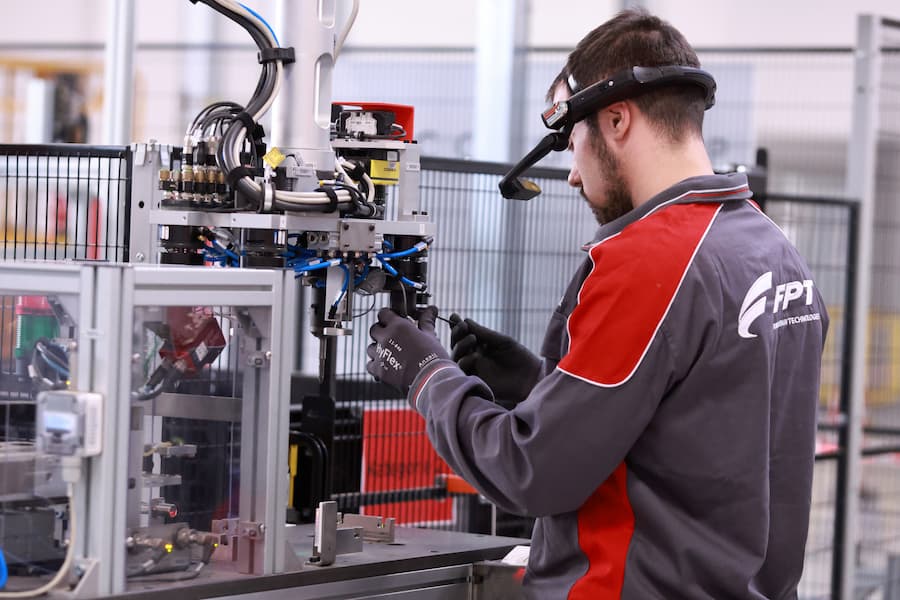
Montata la cover, il pacco batteria è pronto per i test di fine linea, demandati a due macchinari flessibili, in grado di gestire entrambi i design dei pacchi batteria e di svolgere fino a 12 test sul pacco batteria, simulando un breve life cycle. Anche questi banchi sono in grado di recuperare l’energia; il plant, così, si autoalimenta.
Il sistema antincendio prevede degli shelter (enormi ‘scaffali’) posizionati fuori dal plant, nei quali è possibile immergere in acqua un pacco batteria che abbia preso fuoco. L’Msds (Material safety data sheet) è il documento obbligatorio che illustra la gestione in caso di avaria e accompagna la batteria, ovunque si trovi. I pacchi batteria EVO hanno mantenuto la densità energetica della versione precedente e dispongono di più valvole all’esterno, che convogliano i fumi in funzione della stringente certificazione ECE R100.3. L’obiettivo è estendere la vita del prodotto, anche in ottica second life. «Trattiamo due pacchi batterie, con due chimiche (blending) Nmc lievemente diverse, una orientata al bus, con tanti cicli, oltre 6.500, e C-rate più bassi, quindi modalità di carica e scarica più contenute. L’altra ha una chimica orientata alla mobilità urbana, sia per i Daily trasporto merci, che minibus, C-rate che arriva a 2C in scarica, per premiare il profilo di missione del veicolo», prosegue.
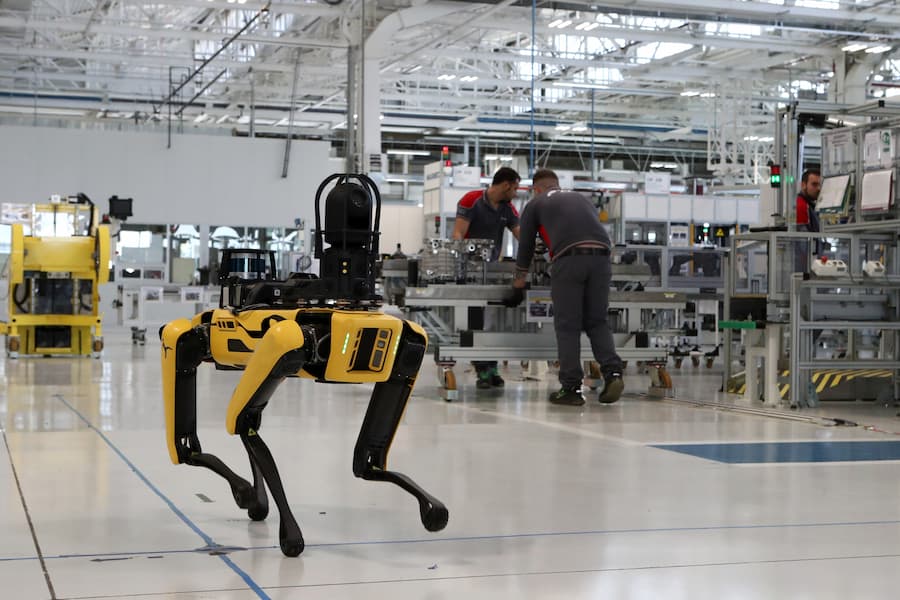
Tra robot e kitting
Prosegue l’alternanza tra intervento robotico e umano. «Dei cobot sono addetti allo spalmaggio della pasta termica e collaborano con gli operatori, per aumentare la capacità e demandare le operazioni ripetitive e potenzialmente foriere di errori umani. È una stazione con tre finestre, adibite al montaggio delle busbar, che permette all’operatore di accedere a una finestra alla volta. In questo modo non entra mai a contatto con tutta la tensione del pacco batteria. Il sistema di visualizzazione lo guida nelle operazioni da svolgere e nel flusso da seguire. Il personale lavora a rotazione per incentivare la versatilità sulla linea».
Ci soffermiamo sull’attività di preparazione dei kit. Un pallet tecnologico è utilizzato per posizionare i componenti, procedere tra le mini-stazioni con il set da assemblare per rendere l’attività ancora più fluida. Il tool che preleva gli oggetti a magazzino è oleodinamico, guidato elettronicamente, preleva e posiziona componenti che sarebbero altrimenti troppo pesanti. Gli Agv prelevano il pallet e lo portano alla stazione di riferimento in maniera autonoma. Legge i data matrix (QR code), avendo una tracciabilità al 100 per cento, i badge code (che si utilizzano sui lotti, per esempio le viti) oppure il sistema di pick to light. La linea degli assali elettrificati ha una configurazione a Y, due linee parallele che convergono in una stazione centrale. La linea di sinistra si occupa dell’assemblaggio dei componenti interni, quella di destra dei componenti esterni, e convergono dove c’è un altro robot antropomorfo che unisce le due parti. Il dressing è un’operazione manuale, con cablaggi, scambiatori, etc. Finito l’allestimento, le propulsioni andranno all’end-of-line.
Quando il gioco si fa pesante
La tappa successiva è la linea heavy-duty, dove si assemblano gli e-axle 840R. «Li montiamo in due varianti: per il mercato nordamericano, destinato al Nikola 3, per quello europeo all’S-eWay, sia fuel cell che Bev» specifica Orsi. Che continua: «Qui sottoponiamo il 100 per cento dei prodotti a cicli di coppia e potenza. Sensori e accelerometri permettono di controllare le vibrazioni e i disturbi acustici dell’assale. Si rimuove l’assale dal banco e si sostituisce l’olio. Il 2% dei componenti è testato a campione sul ciclo vita esteso, tramite Cop (Conformity of production)».
Cool break, prima di addentrarci nella delicata fase di testing, Alice Orsi riassume le coordinate tecnologiche dei prodotti finiti, cioè soluzioni a doppio motore, con motori a magneti permanenti, single speed (una sola marcia), assali di prima generazione per i pesanti.
E l’architettura Salisbury? «Contempla un corpo centrale e i bracci montati con delle viti. Permette flessibilità nell’adattamento al veicolo, perché posso installare il braccio e il sistema frenante richiesti dal cliente e customizzare la parte di accoppiamento con il veicolo, mantenendo il core dell’assale. Il motore è montato parallelamente all’asse ruota, senza coppie coniche, e modularità».
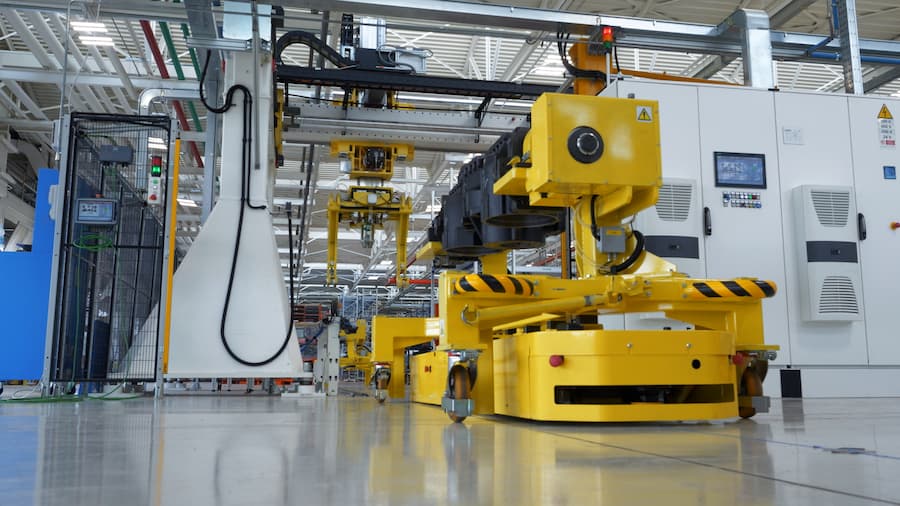
FPT Industrial dispone di tre centri R&D per l’elettrificazione. Torino consente anche attività a livello sistema; Arbon, in Svizzera, per la validazione dei sottosistemi, per esempio, modulo e cella; a Coventry, nel Regno Unito, per il battery management system. Nel corridoio di accesso all’area testing Orsi riprende la panoramica didascalica. «Disponiamo di 74 celle, dedicate all’attività di validazione delle propulsioni in generale, di cui più di 5 esclusivamente per l’elettrificazione. Qui, vedete l’HIL Lab (Hardware In the Loop), centro di raccolta dei dati di validazione degli R&D di FPT, dove questi grandi ‘armadi’ raccolgono le informazioni e ci permetteno di simulare le attività di validazione. Attraverso l’HIL processiamo il software della centralina in assenza del reale sistema hardware. Le celle sono divise in tre macroaree, che corrispondono alla dimensione del motore: pesanti, medi e leggeri. Qualche cella motore sta diventando versatile e si adatta all’ePowertrain. Attraverso uno schema sinottico, cliccando su una cella, visualizzo il test e qualsiasi informazione generica sull’attività in corso».
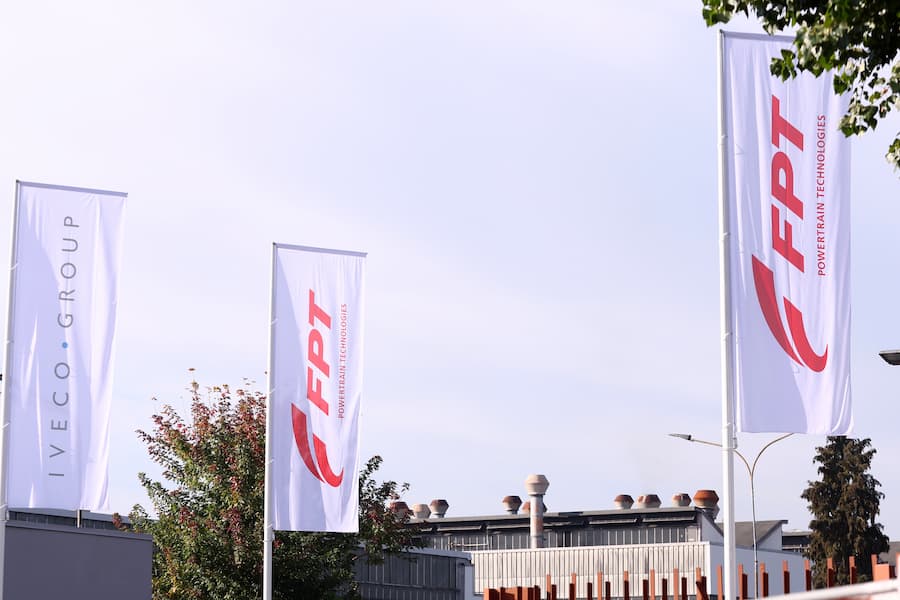
Al cuore dell’e-powertrain
Arriviamo finalmente all’e-powertrain. «La prima cella è la light duty e-powertrain: la central drive è stato uno dei primi progetti gestiti da FPT. Ora ci permette di testare qualsiasi soluzione elettrificata. È equipaggiata con battery emulator da 1 MW, che simulano il funzionamento delle batterie e recuperano parte dell’energia. In questo momento, la cella di fronte è impiegata per mettere alla frusta dei prototipi. I profili di missione sono gli stessi degli endotermici, pur con un diverso impatto sul lato dell’infrastruttura. A intervalli definiti, facciamo degli approfondimenti sui pezzi prelevati dalla produzione».
La cella dei pacchi batteria stuzzica la nostra curiosità. All’interno ospita una camera climatica e un banco prova per simulare le condizioni termiche. «Possiamo testare fino a tre batterie da 69 kWh, simulando condizioni ambientali differenti. È una camera climatica ‘walk-in’ e dispone di un antincendio e di diversi sistemi di sicurezza. Collegandosi alla batteria si possono leggere i segnali relativi a prestazioni, sicurezza, condizioni ambientali. Un esempio? L’invecchiamento del pacco batterie. Alcuni test sono assai invasivi, i cosiddetti ‘abuse test’: si innesca la propagazione termica della batteria e si verifica la resistenza all’acqua. Ad Arbon un gruppo di lavoro è dedicato alle celle, con una grande profondità di dettaglio nella lettura di determinati segnali». Sarà cambiato qualcosa nell’approccio metodologico, dalla inaugurazione dell’e-plant? «In generale» ci risponde Orsi, «nella prima generazione di prodotti prendevamo i moduli dai fornitori per svolgere il lavoro di integrazione, nel quale siamo estremamente competenti, e creare valore aggiunto. Portarsi le celle in casa comporta una elevata complessità tecnologica, dovendo gestire dei processi chimici. Ad oggi è meglio procedere per gradi e avere la possibilità di fare scelte che favoriscono la competitività tecnologica».
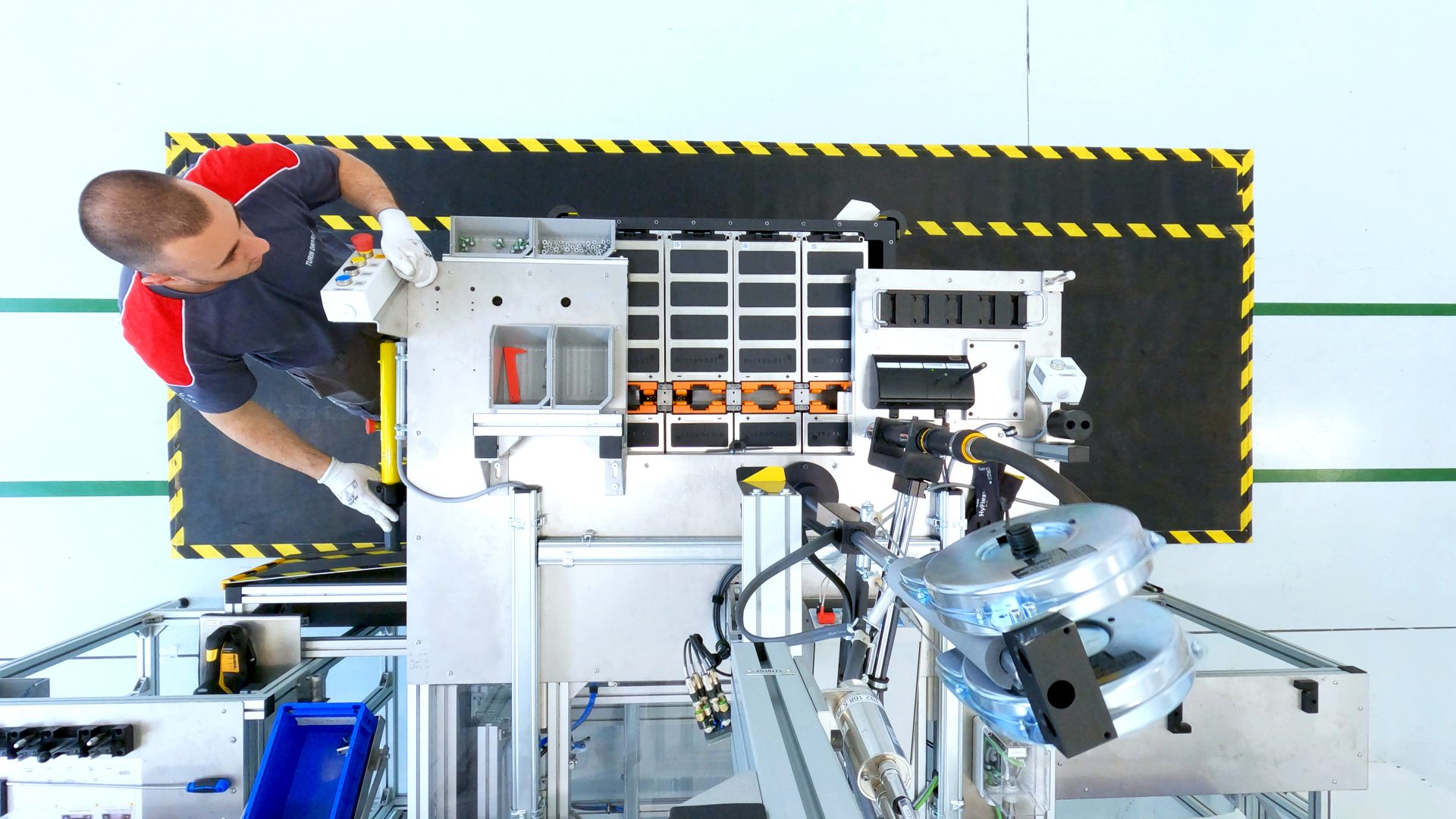
FOTO
Dentro il battery lab
Consentitici una digressione sul laboratorio delle batterie. Cosa deve avere un costruttore di pacchi batteria per essere sempre sul pezzo? «Un laboratorio di prototipazione dei pacchi batteria. È quello che succede in questo e-plant. Degli specifici carrelli ci permettono di fare prototipazione. Sono equipaggiati con un piano semovibile che permette di abbassare il pacco batteria, nel caso di una propagazione di fiamma, e inserire acqua da appositi bocchettoni. Annego il pacco batterie nell’acqua, per due motivi: abbasso la temperatura e rimuovo l’ossigeno, bloccando la reazione chimica.
In quest’area prendiamo il componente, assale o propulsione elettrica, lo assembliamo nella configurazione che intendiamo validare o testare, e lo fotografiamo, per avere una documentazione fotografica antecedente alla prova. Disponiamo di un laboratorio meteorologico in cui effettuare misure di sottocomponenti. Talvolta, soprattutto, in fase di validazione di prodotti nuovi, li controlliamo con sensori termici, accelerometri e altri oggetti di sensoristica che aggiungono informazioni a quelle fornite da banco prova e centralina. Alla fine della prova il procedimento sarà inverso. Rimossa la strumentazione, si verificano le informazioni visive attraverso un report fotografico e si procede al teardown… e alla eventuale misurazione di alcuni componenti. L’ultimogenito della nostra famiglia di laboratori è il Tcu Lab, abilitato alla validazione della trasmission control unit». Ed è così che un assale elettrificato e un pacco batterie si accreditano alla trazione dei veicoli commerciali. Succede in casa di FPT Industrial.
Fabio Butturi