MANUTENZIONE OGGI / Organizzare, organizzare e ancora organizzare…le officine
Si conclude qui la rassegna delle funzioni di manutenzione descritte nell’ambito del Regolamento europeo 779/2019 che, sebbene destinato al settore ferroviario, trova ampia e confermata applicabilità quale metodo a livello generale per identificare i soggetti coinvolti nella catena del valore di questo complesso processo. 1. Manutenzione oggi, il fleet manager nelle aziende tpl: il mio […]
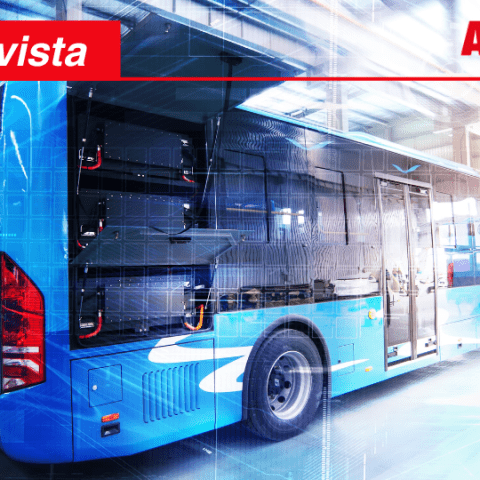
Si conclude qui la rassegna delle funzioni di manutenzione descritte nell’ambito del Regolamento europeo 779/2019 che, sebbene destinato al settore ferroviario, trova ampia e confermata applicabilità quale metodo a livello generale per identificare i soggetti coinvolti nella catena del valore di questo complesso processo.
1. Manutenzione oggi, il fleet manager nelle aziende tpl: il mio ruolo che cambia
2. MANUTENZIONE OGGI / Perché lo “sviluppo” è un pilastro
3. MANUTENZIONE OGGI / Interagire per gestire…bene.
4. La quarta (e ultima) funzione della manutenzione
Nella disamina delle precedenti funzioni della manutenzione nel tpl si sono analizzate l’organizzazione a livello di processi e Kpi, il coordinamento delle attività, l’analisi dei dati e le relazioni con l’esercizio; tutti aspetti essenziali che condizionano le operazioni di manutenzione rendendole efficienti oltre che efficaci. Viene ora finalmente il momento di trattare i veri protagonisti: le officine di manutenzione. La quarta funzione, chiamata ‘esecuzione della manutenzione’ è sovente esternalizzata come in ferrovia, con un fenomeno qui ancor più pronunciato perché risalente a circa 20 anni prima, quando negli anni Ottanta i contratti collettivi nazionali degli autoferrotranvieri risultavano estremamente penalizzanti rispetto a quelli delle officine di autoriparazione, che nel frattempo erano cresciute e si erano diffuse nel mercato anche per i veicoli pesanti. Ad oggi il corretto mix proprio del ‘make or buy’ di manutenzione è diventata un’abilità riconosciuta sebbene ancora non diffusa, e si è stabilizzato un modello nel quale le aziende di ridotte dimensioni fanno ampio ricorso alla manutenzione esternalizzata mentre quelle che dispongono di flotte dai 100 autobus in su hanno un’organizzazione interna in grado di svolgere almeno alcuni interventi di base e in ogni caso di sovraintendere al processo di manutenzione mediante le tre funzioni già analizzate in precedenza.
Ancora diversa è la situazione dei grossi player con più di 1.000 autobus, che pur affidando la manutenzione all’esterno dispongono di vere e proprie società di manutenzione controllate che operano con contratti inter-company che rispondono in toto a logiche di mercato.
Il tema è disciplinato in Italia dalla legge 122/92 (poi aggiornata 22/12) rappresenta il cardine attorno al quale ruota l’organizzazione di un’officina. In accordo con tale dettato, sono due i requisiti obbligatori per un’officina: la presenza di un responsabile di manutenzione il cui nome è riportato presso la Camera di Commercio, in possesso di specifici requisiti di idoneità e competenze; la disponibilità di personale interno debitamente formato secondo le tre professioni riconosciute di meccatronica, gommista e carrozzeria.
È importante ricordare come l’iscrizione alla Camera di Commercio sia obbligatoria non solo per quei soggetti che vendono sul mercato le proprie prestazioni di autoriparazione (scenario ‘buy’) ma anche per coloro i quali svolgono servizi di trasporto pubblico locale e dunque i utilizzano i propri veicoli nell’ambito del processo di core business; anche in questo caso le loro officine (scenario ‘make’) devono sottostare alla medesima disciplina.
Lo scenario è oggi reso più complesso da una maggiore articolazione delle competenze che deriva dalla diffusione di tecnologie di propulsione differenti: la riparazione di quelle a metano fa capo a norme Iso, En e Uni specifiche e di recente riformulazione; la propulsione elettrica richiede a sua volta una procedura di gestione dei lavori elettrici conforme a quanto previsto dalla norma Cei 11-27 e della relativa linea guida applicativa edita dallo stesso Comitato Elettrotecnico Italiano.
Volendo partire da zero
Il periodo corrente vede cambiamenti consistenti in corso e non è raro vedere la creazione di nuove officine o ‘point of service’ mono e multimarca. Il fenomeno è incentivato sia da capitolati di full service previsti specificatamente nelle gare per l’acquisto di nuovi veicoli elettrici, sia da investimenti privati Un’officina di manutenzione per autobus è un ambiente cruciale per garantire la sicurezza, l’affidabilità e la durata della flotta di autobus.
Di seguito, una sintesi dei principali aspetti da considerare per organizzare un’officina di manutenzione autobus in modo efficace e al passo con i tempi.
Spazio e layout partire da zero
Il layout dell’officina deve essere progettato con attenzione per ottimizzare l’uso dello spazio e consentire il movimento agevole degli autobus e del personale. Le aree chiave includono:
1. Area di lavoro: questa è la zona principale dove vengono eseguite le operazioni di manutenzione. Dovrebbe essere sufficientemente ampia per ospitare più autobus contemporaneamente e dotata di attrezzature necessarie, come sollevatori (l’utilizzo delle fosse è in corso di graduale abbandono), strumenti e stazioni di lavoro. Si ricordi come molte lavorazioni sui veicoli moderni avvengono oggi sul tetto, con ciò richiedendo scale idonee e linee vita.
2. Area di stoccaggio: uno spazio dedicato per immagazzinare pezzi di ricambio, oli, lubrificanti e altri materiali necessari per la manutenzione. Deve essere organizzato in modo da facilitare il reperimento rapido e la gestione dell’inventario.
3. Zona di ispezione: Quest’area è riservata all’ispezione iniziale e finale degli autobus, dove si controlla la qualità del lavoro svolto. Si tratta di un’area presente nelle officine multicliente (sovente coincidente con la cosiddetta ‘accettazione’) ma pressoché sconosciuta nella manutenzione interna.
4. Uffici e spazi di supporto: questi includono uffici per il personale amministrativo e spazi per il personale tecnico per pause e riunioni. Le aule di formazione non dovrebbero essere trascurate ma anche in questo caso si tratta di spazi rari a trovarsi.
E c’è dell’altro…
Un team ben formato e addestrato è essenziale per l’efficacia dell’officina. È importante avere diversi ruoli, tra cui meccanici specializzati, elettricisti, responsabili della logistica delle parti di ricambio e supervisori. Una pianificazione delle risorse umane deve tenere conto dei turni di lavoro, dell’orario di manutenzione preventiva e delle emergenze. Sarebbe qui fin troppo facile parlare genericamente di risorse formate: quello che occorre è passare ad un “sistema di acquisizione e mantenimento delle competenze” basato sull’analisi dei rischi (da condursi a livello di veicoli e sottosistemi) per individuare, di volta in volta, gap e i conseguenti piani di formazione specifici
La manutenzione preventiva è in teoria cruciale per prevenire guasti costosi e tempi di inattività improvvisi. Tuttavia, le officine sono più assimilabili a posti di pronto soccorso che a reparti di degenza nei quali è facile programmare le cure dei pazienti: un gestionale software di programmazione delle manutenzioni deve a maggior ragione essere implementato, includendo ispezioni regolari, sostituzioni di parti soggette a usura e servizi di routine, proprio per evitare di concentrarsi sulle ‘emergenze’.
Un’efficiente gestione delle parti di ricambio è fondamentale per evitare ritardi dovuti alla mancanza di materiali. Un sistema di gestione del magazzino (previa formazione delle risorse dedicate) dovrebbe essere adottato per monitorare le quantità di parti di ricambio disponibili, pianificare gli ordini e ridurre al minimo i tempi di inattività causati da pezzi mancanti. Questa è tuttavia proprio una delle criticità lamentate in molte organizzazioni del settore, per la presenza di risorse dotate di scarsa preparazione di base.
L’adozione di tecnologie moderne può migliorare ulteriormente l’efficienza dell’officina. L’uso di sistemi di diagnosi computerizzati, monitoraggio delle prestazioni e software di gestione dell’officina semplifica già il lavoro dei tecnici e migliora la precisione delle riparazioni, me esiste tutta una fascia di ulteriori tecnologie connesse (sistemi laser per la convergenza, distributori automatici di fluidi funzionali…) da adottare, fra l’altro oggetto di agevolazioni fiscali mirate.
Progettare ex novo o riorganizzare un’officina di manutenzione per autobus richiede una pianificazione attenta e una considerazione approfondita di vari aspetti. Un layout intelligente, una squadra ben addestrata, una gestione delle risorse efficiente e l’implementazione di tecnologie avanzate sono tutti elementi chiave per garantire un funzionamento fluido, costi ridotti e tempi di inattività minimi.
Alessandro Sasso, presidente ManTra